What was the project?
We had to create a building out of spaghetti and blue-tack that could withstand a 10 second earthquake. In groups of 2-3, we had to prototype, design and build a structure:
- A minimum 60cm tall
- Maximum 30cm base
- A budget of $60
- Has a 5x5cm square at the top.
- Can endure 10secs of vertical and horizontal shaking without toppling over or breaking.
- 1 gram of blue-tack is $1 and 1 spaghetti strand is $1.
We researched design features used in real life by engineers to make buildings earthquake resistant so we could mimic those techniques and first-hand see how they work.
Engineering Process:
- We assembled ourselves into groups of 2-3 and assigned roles to each other based on our qualities. (Eg. team manager, communicator etc.)
- We researched different techniques and structures of buildings engineers used in real life to help buildings withstand earthquakes.
- Then, we drew a labelled diagram with how much of each material we needed, explanations of which design features we used and why, and then predicted how our building would withstand in the ‘earthquake’
- Following our diagram, we built our first prototype and tested it by shaking the board and seeing what would need improvement. The building was overall pretty stable but we needed to fix the top part which was tipping to the side.
- After our first test, we looked at what needed improvements in the prototype and altered some features (the top level of the structure) to make it more durable and budget friendly. We also added some support beams to help it stay still.
- Then, we tested it for the 2nd time and added a few alterations so it wouldn’t tip from side to side.
- We tested it for the last time and settled on our final product.

What would I change to the process?
Something I would change is that instead of making individual diagrams from each team member, we should just combine onto one. It was useful to have our own research because we had different techniques we could contribute however if we just all combined it into one diagram, I think it could have saved a lot more time to leave for actually building the structure.
Another thing I would change to the process was that sometimes when we left our in-progress building on the table and we came back the next day, the structures would be broken and the blue-tack and spaghetti that we measured out would be gone.
Additionally, we found that it was really difficult sometimes to keep the spaghetti into the blue-tack joints because the blue-tack would stretch or melt. If instead we had marshmallows to stick the spaghetti into, I think it would be way easier to make the structure and also save time.
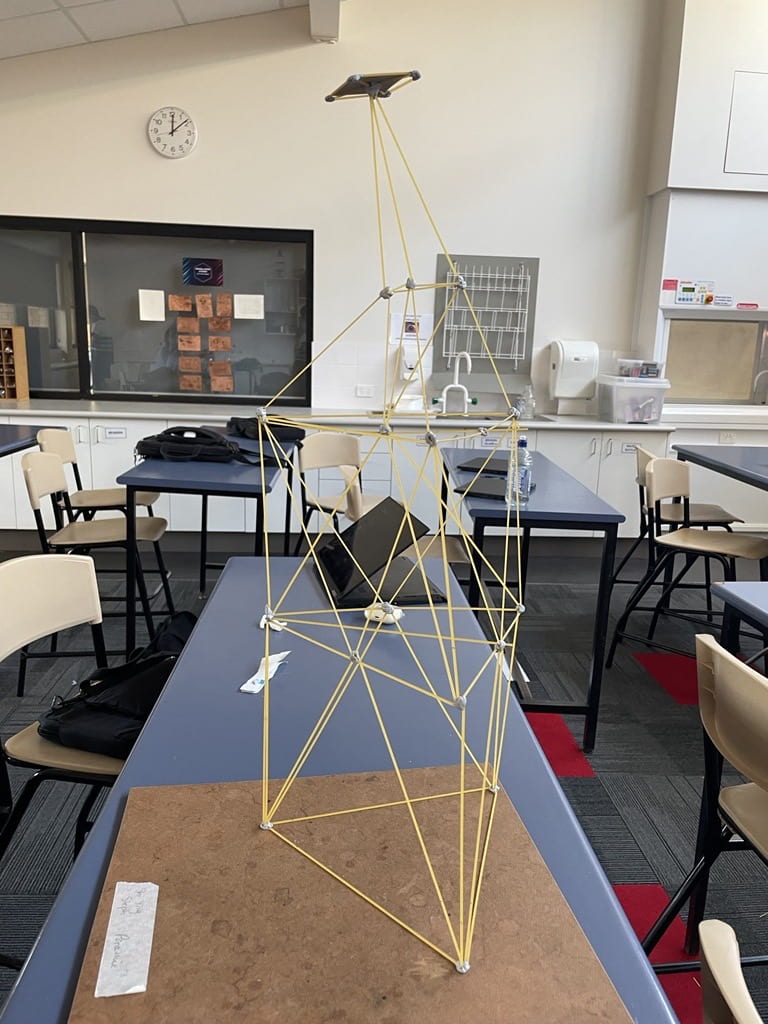
Teamwork and Collaboration:
In my group was Stephanie, Paramie, and I. We assigned each other roles
Stephanie:
We gave Stephanie the role of speaker because she communicates well and understands what’s going on so she can ask for help when we need it. She’s willing and comfortable to ask for help from others.
Paramie:
We assigned Paramie equipment manager because she’s a very organised and responsible person. She makes sure that we have the right materials and ensures we clean up afterward.
Shi Ying:
We gave Shi Ying project manager/reporter because I’m efficient with time management and make sure everyone’s contributing somehow. I make sure that everyone has their individual and team aspects finished within the time frames and make sure everyone knows what’s going on.
I think that overall, our group collaborated really well and worked efficiently together. Everyone contributed and did their part to make sure they didn’t drag the team down and we supported each other and worked together especially when building the prototypes, sending each other images/videos, and updating what stage of the process we’re at if someone missed a lesson.