Summary of the Project:
Our group was assigned the task of designing an earthquake-resistant building that could withstand a fabricated earthquake, using only spaghetti and blue tack. However, there were certain limitations and parameters that were set, which included:
- is quick and easy to assemble
- has a minimum height of 60 cm
- has a maximum base of 30 cm x 30 cm
- has a flat platform on the top level of at least 5 cm x 5 cm
- remains standing after an earthquake, as simulated by shaking a table for 10 seconds
We also had to stay within our budget of $60, where every piece of spaghetti was $1 and every gram of blue-tack was $1.
The Engineering Process:
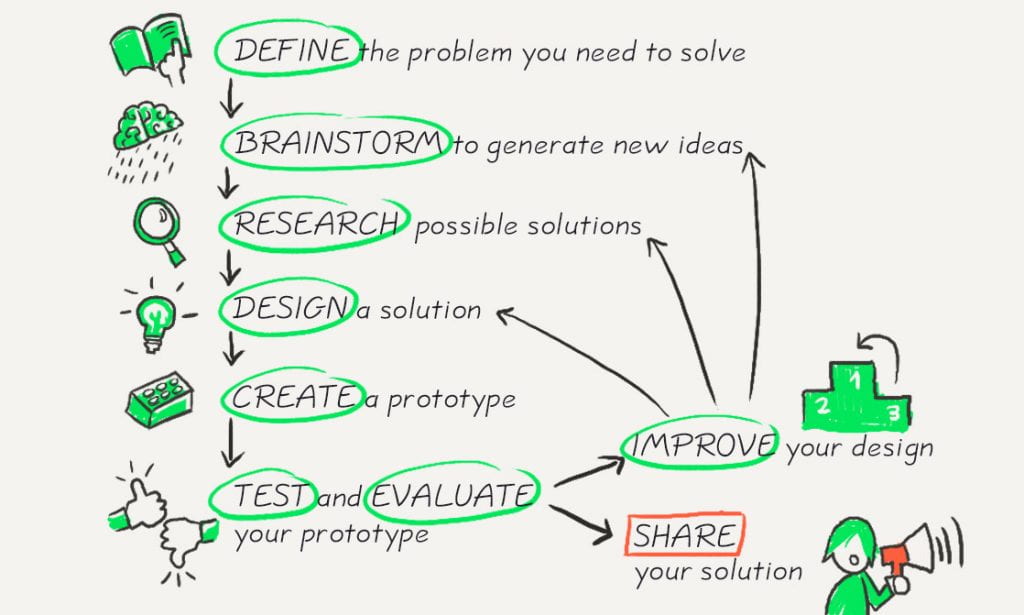
We looked at towers from all around the world, including the works of Shigeru Ban. Our research concluded that the three main features we would need in an earthquake-resistant tower would be a strong base, cross braces, and triangular shapes all around. Using this we developed a design:
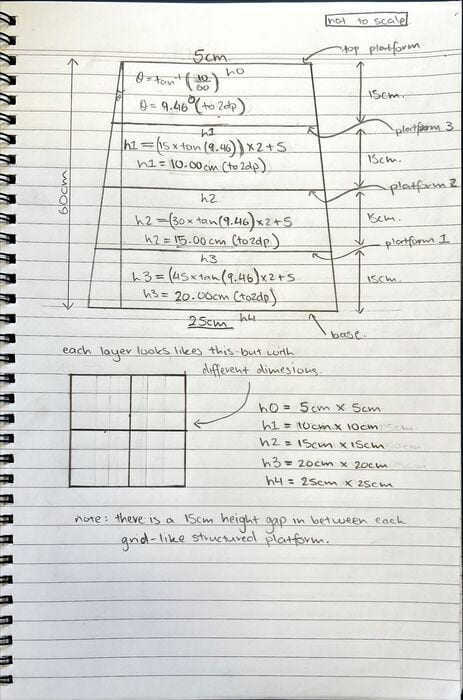
After making a design, we started to create our first prototype. At first it started off as fine, as were able to build the first and second layers comfortably. However, we ran into a few problems:
- As we go up the structure, the spaghetti gets smaller and weaker
- We miscalculated the amount of bluetack we would need
- We would need more cross braces for stability, due to the diagonal nature of our design
Due to these problems, we decided to rebuild. In our second design, we opted for a simplistic approach with a cubic structure, as it fixes the problems above, using less of the resources. This is what our prototype looked like:
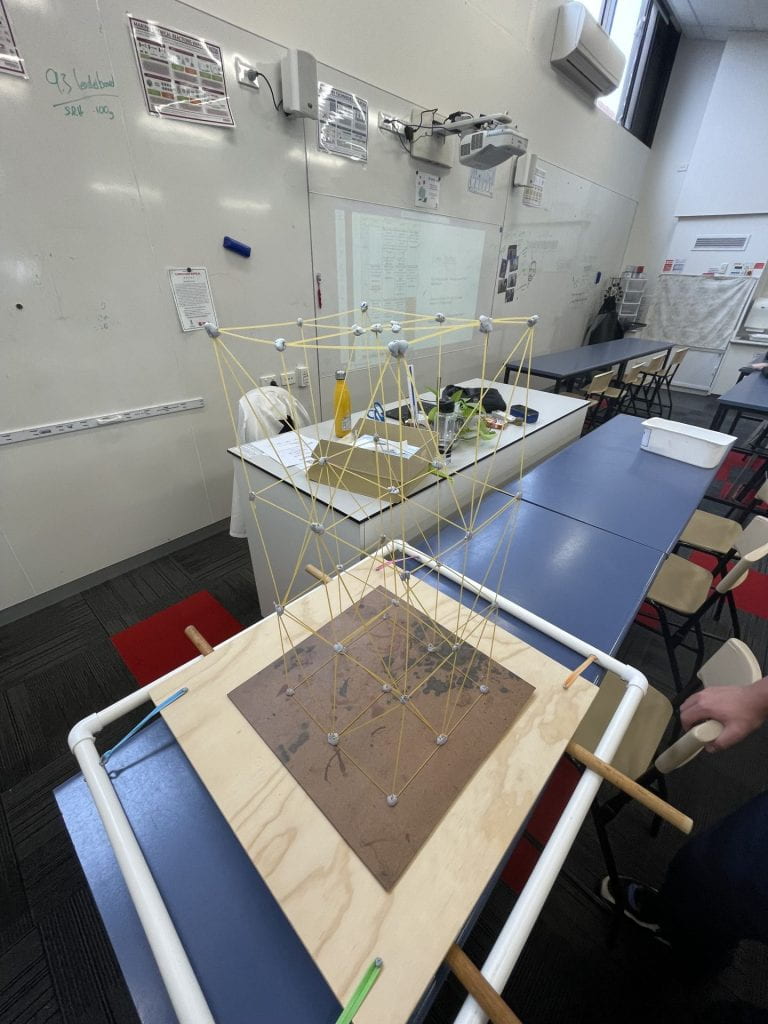
For our second prototype, we added more braces going into the middle for even weight distribution:
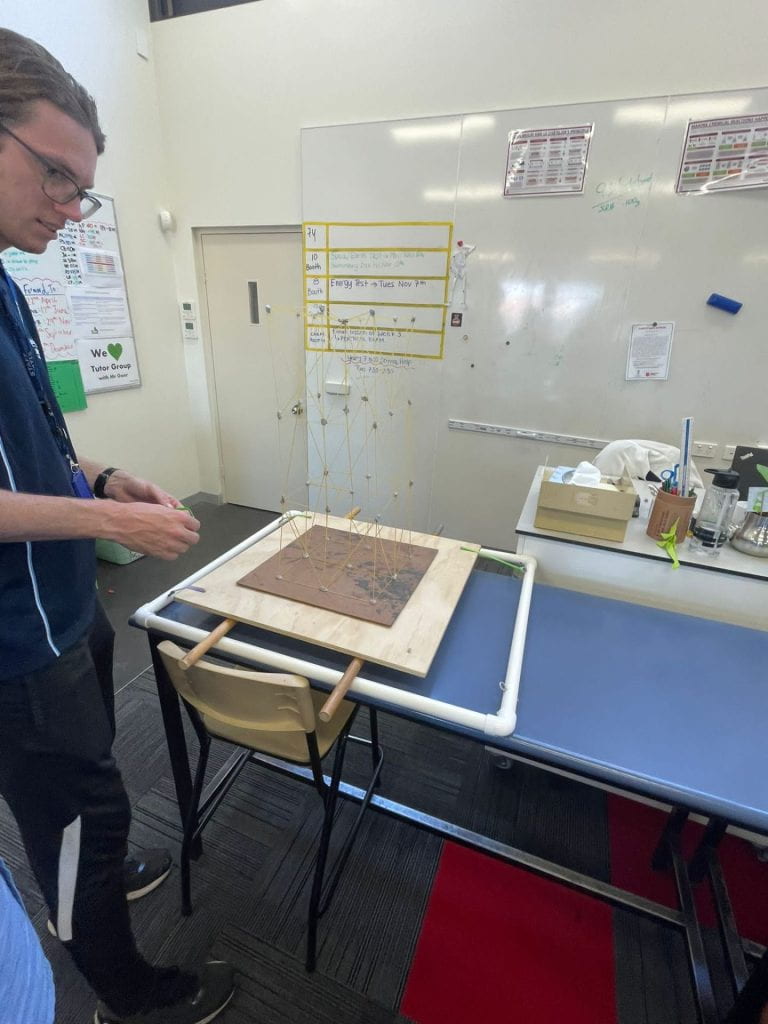
If we did this again, I would make sure that we set ourselves more realistic, achieveable goals and designs because even though the first design looked very good, it was very complicated and there was a lot that could have gone wrong. We also should have had more planning and research beforehand.
Collaboration:
In our group, each of us had assigned roles in order to make this process more efficient and organised. For the project, Rithvik was chosen to be the project manager, which is the person who keeps everybody on track and takes the lead. Jacob was considered to be the equipment manager, who helped to organise our materials and make sure we were within budget. Finally, I was the designated speaker and reporter, who sought help if we needed it and made sure we were ready to present on time. However, we all interchanged our roles throughout the process. Rithvik’s creativity and passion for engineering, Jacob’s ideas and organisation, and my research and planning all contributed to delivering a functioning prototype.